Additive Manufacturing in Product Development Processes
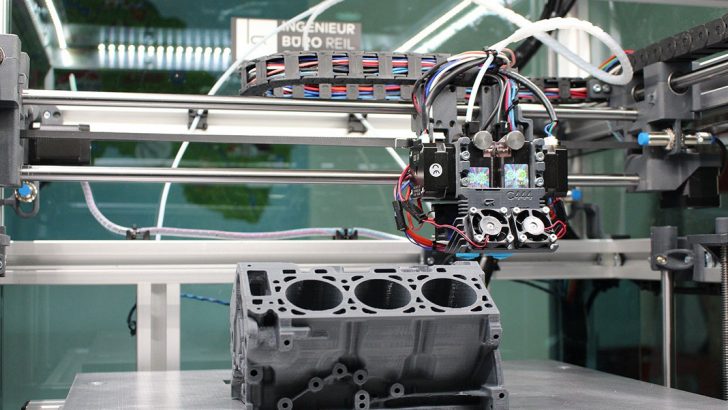
Additive manufacturing is becoming a fixture in many product development processes. Now comes the challenge of making it more scalable.
Additive manufacturing has transformative potential to revolutionize manufacturing and take it to new heights of production and efficiency. For the time being, however, it’s an approach still rife with unanswered questions.
Manufacturers want to experiment with additive manufacturing, but they might wonder whether it’s scalable enough to meet present and future volume demands. Additionally, they’re concerned about how many 3D printers it will take to satisfy production quotas — and whether those printers can consistently meet quality standards. Overall, product developers assess their strategic objectives and try to determine how much value additive manufacturing actually provides.
Those questions are important, and the answers are complex. Additive manufacturing’s ubiquity in product development depends on achieving economies of scale to reduce material and equipment costs, but the industry’s ability to clear those hurdles remains to be seen. What is clear, though, is the theoretical impact of additive manufacturing on product development is already becoming a reality.
Additive Manufacturing Applications and Innovations
Additive manufacturing’s biggest hindrance right now is obvious: conventional manufacturing’s continued viability. After decades of a tried-and-true product development process, manufacturers are keenly aware of what does and doesn’t work. In most cases, additive manufacturing hasn’t presented a compelling enough use case for manufacturers to do things differently — at least not yet.
One notable exception, however, is related to additive manufacturing innovation. As an emerging means of production, additive manufacturing has a wealth of room to grow in unexpected directions. Many of those directions will prove to be false starts, but others may redefine manufacturing for the future.
Now, compare the potential of additive manufacturing to the outlook for conventional manufacturing. Assembly lines can incrementally improve their speed, productivity, quality, and countless other metrics, but they will struggle to discover innovative breakthroughs that elevate what’s possible. Those breakthroughs are things of the past for conventional manufacturing, but they represent the future of additive manufacturing.
Better Your Additive Manufacturing Product Development
We can’t expect just those innovations to appear on their own — or for additive manufacturing to mature without a lot of effort. We also can’t expect manufacturers still questioning 3D printers to embrace them without some certainty the effort will pay off. With that in mind, use these three strategies to manage the development of products that use additive manufacturing.
- Build process-focused teams rather than product-focused ones.Consider rearranging personnel teams to focus on manufacturing processes rather than specific products. Lay out manufacturing plans for different products, see which ones can incorporate 3D printing, and create teams that support the necessary technologies rather than have specific ownership of given products.
- Devote time to part validation.Give equal consideration to the qualification/certification of additive-manufactured parts, especially for critical applications. Start by considering the viability of building various parts with 3D printers. If you can build them, weigh whether using a 3D printer would be cheaper or more efficient than conventional approaches. Finally, ask whether the quality of 3D-printed parts will be as good as — or better than — conventional processes.
This goes back to the developing standards and certifications for additive manufacturing in many industries (particularly aerospace). Strict quality controls haven’t been a priority absent those standards, but those quality controls are necessary and likely coming shortly. Manufacturers can get ahead of this issue by considering the complete triangle — viability, efficiency, and quality.
- Conduct “virtual prototype testing.”This testing will help reduce blind alley designs by keeping nonviable designs restricted to the drawing board. With a virtual prototype test software, digital design files can be tested with different materials to help determine whether each design is feasible.
Different types of additive manufacturing have different strengths and weaknesses. Concluding whether one or another is suitable for product development isn’t a simple process. Virtual prototyping avoids unnecessary waste and helps manufacturers uncover every opportunity to leverage additive manufacturing applications and innovations as they continue to develop.
Those applications will be even more critical as the pandemic’s impacts on conventional manufacturing continue to persist. As new manufacturers experiment with additive manufacturing and develop their own viable applications, we move closer to achieving economies of scale. This could be the tipping point for this emerging technology and a major step into the Fourth Industrial Revolution.
Source: Animesh Dey | industrytoday